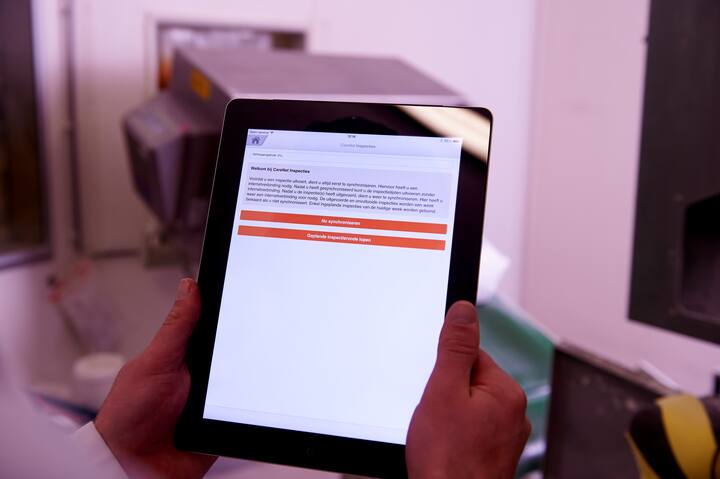
Cavalier about Normec Foodcare Online
Cavalier takes the step towards QA digitization
Cavalier develops and manufactures chocolate products without added sugars. The company began digitizing its quality control processes at the beginning of this year. In an interview, Felix Verdegem, CEO of Cavalier, discusses the necessity of digitization and the benefits it has brought to the company.
Why did you want to switch to QA digitization?
“We were using different systems for documentation, executing and following up on action points, keeping track of inspections, etc. Within our quality department, there was a need for a system that could fully meet our requirements in all areas," says Felix. Cavalier first submitted a demo request to view the features of our software. Shortly after the request, the demo appointment was scheduled by our sales managers. During the demo, the various modules were shown and the various features and possibilities of the software were explained.
Quick switching
The company wanted to move quickly and implement the system within the same week. Our account managers and implementation consultants ensured that the Inspections, Manual, and Specifications modules could be implemented within the same week. During the implementation days, they ensured that the modules were set up appropriately for the company and provided extensive training on how to use the modules.
We have nothing but praise for the speed with which your colleagues in both Belgium and the Netherlands have helped us.
Cavalier about Normec Foodcare Online
“The implementation had to be done very quickly, and we have nothing but praise for the speed with which your colleagues in both Belgium and the Netherlands helped us. The training courses were well structured, and the implementation consultants had the necessary expertise or could fall back on their colleagues if necessary. The colleagues were also very flexible.”
“Working with Normec Foodcare Online software gives our company a much more structured approach to quality control. The manual module provides a clear overview of all the forms and manuals that are used on a regular basis. This makes it much easier to find, consult, and update everything when necessary.
The logically structured specification module is a very useful tool for building an end product from the basic ingredients to the packaging. For us, it forms the perfect network between the various departments involved in setting up a new product (purchasing, quality, packaging, sales, logistics, and marketing). In addition, the allergen module that is integrated into this is a useful tool for quickly determining whether a colleague has accidentally made a mistake when using new ingredients in terms of new allergens. This module also makes it much easier to calculate nutritional values. In fact, it is an almost comprehensive module for the technical aspects of a product. Finally, the inspection module is simple and easy to use and currently guarantees us good follow-up of all types of inspections, checks, and audits in the area of quality within our company. This is certainly due to the aspect of extra control over the tasks performed, inspections, etc."
“The quality department no longer has to spend so much time on organizing, setting up, and following up on inspections and checks, and can find everything much more easily. In addition, the verification system ensures that there is always a double check of the actions and checks to be carried out. This greatly reduces the risk of errors and omissions.
During audits, the online manual provides a solid reference for the quality manager and allows auditors to find everything they need almost independently, without assistance if necessary. This gives auditors the opportunity to focus on the issues that really matter in an audit, rather than getting bogged down in procedures that may or may not be in order.
The Specifications module serves as a framework for everyone within the company who is involved in specification management, from the development and elaboration of new products from a basic ingredient to the final product. The ultimate responsibility lies with the quality department for the final check.
The introduction of the QA software also provides a much clearer indication of where there are still ‘shortcomings’ or where more attention needs to be paid based on clear action points arising from the inspections. The follow-up of the action points is also guaranteed by the entire system with control and reminder mechanisms."
The introduction of the QA software also provides a much clearer indication of where there are still ‘shortcomings’.
“The software certainly offers advantages, such as a clear structure in one place, which means that much less time is lost searching for specific items. An overview of action points per type of inspection or audit can be quickly presented to the auditor. Direct digital reporting reduces the risk of potential defects being concealed and ‘forces’ everyone in the company to comply more closely with quality requirements. The presence of templates for different types of audits in the system is a great help in preparing for an audit."
“The software is very user-friendly for people with all kinds of educational backgrounds. It takes little effort to learn how to use the three modules we work with. In addition, there is good follow-up from time to time to further optimize its performance.”
Working with the software gives our company a much more structured approach to quality control.
More about Normec Foodcare Online
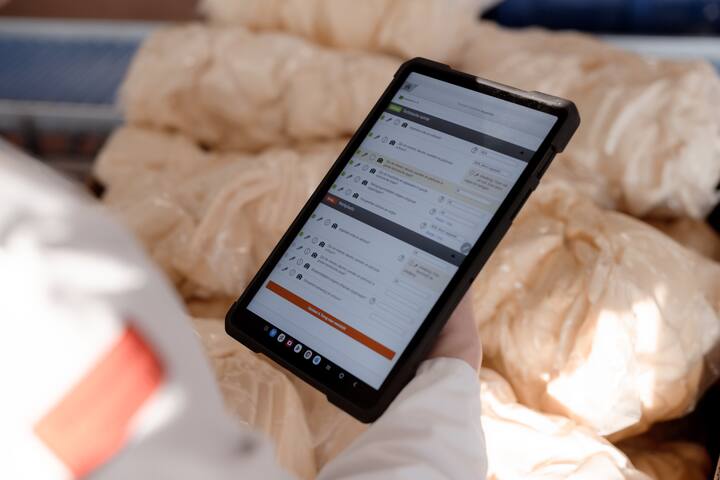
Normec Foodcare Online
's-Hertogenbosch Netherlands