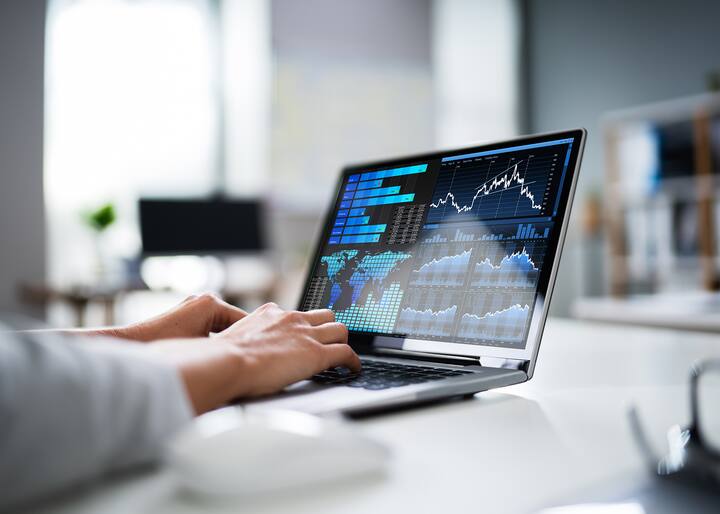
SanLucar about Normec QC One
“Our quality inspectors work with QC One software at various locations worldwide.”
More and more retailers are choosing SanLucar fruit and vegetables for their shelves. This is due to the high quality standard of the products. The Spanish company behind the premium brand has complete control over the production chain through its own cultivation and applies very strict quality guidelines. Antonio Soria, quality technician at SanLucar: "We leave nothing to chance. We now work with QC One software at various locations worldwide."
Top quality
A freshly picked citrus fruit from grandma's garden. There's nothing that tastes better. At least, that's what Stephan Rötzer thought when he founded SanLucar in sunny Valencia in 1993. His dream was to grow fruit and vegetables that tasted as if you had just picked them yourself. Thirty years later, his company has around 3,400 employees in more than 30 countries and the widest range of top-quality products on the market, including fresh fruit, vegetables, smoothies, freshly cut vegetables, flowers, plants, and ice cream.
From sowing the seeds to delivery to supermarkets, SanLucar adheres to very strict quality standards. All their products are checked several times after harvesting. Only the best are packaged and labeled according to strict quality standards before beginning their journey to the supermarkets.
Careful selection
Antonio Soria, quality engineer at SanLucar, who is responsible for translating process optimization into QC One together with the IT team, explains that quality is paramount at SanLucar. “Our company carefully selects its partners. From growers and sales channels to external parties that support our production processes.”
According to the Spaniard, as a large international company with production all over the world, they needed a powerful and innovative system that would enable them to work on the quality of their products in a cyber-secure and data-driven way with a view to the future. “We ended up with QC One through a global tender.”
Smart software
SanLucar uses the Dutch software system QC One at various locations. "The number of locations using it is growing, partly because we are growing. We also use the software in the office to check claims on labels and to verify that all quality controls have been carried out correctly. The system provides us with all conceivable information about suppliers and products, which fits in seamlessly with our data-driven culture. Thanks to the app, our quality inspectors on site can carry out export, import, stock, and shelf life inspections. During the inspections, all the tools they need to draw up a complete and professional report are available in the app. A handy feature is a scan function, which uses a barcode scan in the app to immediately create an inspection report from our ERP system.
Antonio also praises the fact that QC One enables him to train (new) employees to speak the language of quality and incorporate the jargon that has been used at SanLucar for many years into the software.
Brand-specific standard
SanLucar's quality controllers now use all available QC One functions in their quality checks. From the moment the software is installed, the same quality standard applies to all parts of the production chain, and the templates can be adapted to the relevance of that specific point or type of inspection. "This is fully guaranteed and supported by the software. In the app, packaging types, labels, and codes are an integral part of an inspection report and registration. QC One enables us to manage all product specifications and translate them into inspection templates with our brand-specific characteristics," says Antonio.
Working more efficiently
According to Antonio, QC One is a highly flexible system that is designed to meet current quality requirements. The system also enables SanLucar to work in a data-driven manner. “We have moved from a reactive to a proactive approach. This gives us more control over our product quality,” he explains.
QC One now determines the process standard. The app provides feedback directly to the ERP system. “All this makes our work so much more efficient than before. It's incredible how many of our requirements have been integrated into the system. And we continue to optimize things together. We can't imagine working without this system anymore.”
Pursuing goals
Antonio concludes by saying that he would recommend working with QC One to anyone. “The personal collaboration with the QC One team is fantastic. We are a demanding client, but it just works really well between us. The people at QC One know exactly where our priorities lie. That makes it very pleasant to work with them. It certainly helps us pursue our goals.”
Discover the benefits of QC software
Would you also like to gain more control over your sales market and benefit from the advantages of QC One for your organization? Request a free demo now and discover how the smart QC One software can help you optimize quality and strengthen consumer confidence.
More about Normec QC One
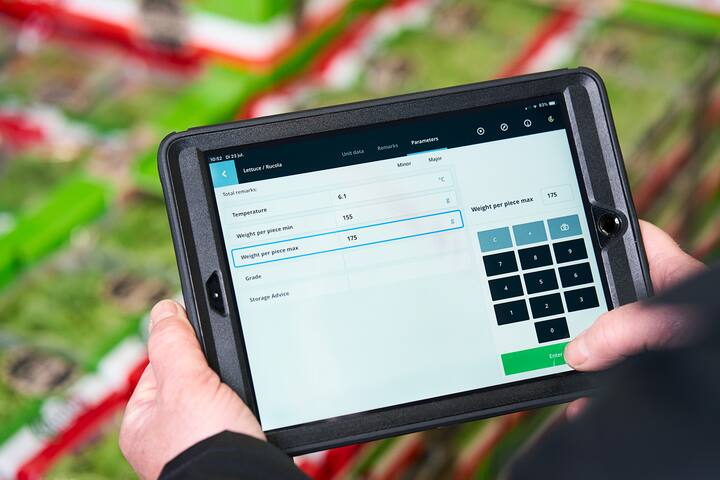
Normec QC One
Poortugaal Pays-Bas