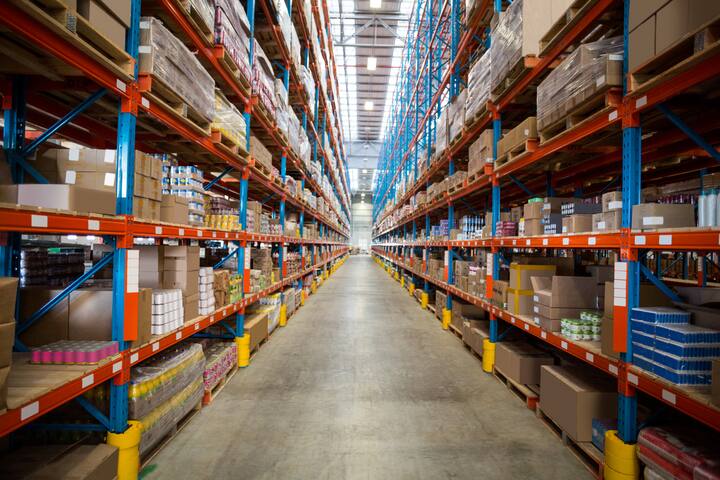
Nico Sluis Vleeswaren about Normec Foodcare Online
Nico Sluis Meat Products chooses the highest level
Manually compiling reports is really a thing of the past. Nico Sluis Vleeswaren has automated these kinds of processes with Normec Foodcare Online's online QA system. “In this system, all data is linked together, and with a single click, we have the right reports and analyses,” says director Nico Sluis. “This saves us a lot of time.”
Automation
“Nico Sluis Vleeswaren has always been at the forefront of automating its quality management system,” says Business Unit Manager Rick Veldkamp of Normec Foodcare Online. "This makes the company a real exception in the industry. Around 90 percent of food companies still carry out mandatory registrations, such as inspections, on paper. Employees enter their findings into Excel, and reports are also created manually."
Around 90 percent of food companies still carry out mandatory registrations, such as inspections, on paper. Employees enter their findings into Excel, and reports are also created manually.
Links
At the end of 2015, Nico Sluis Vleeswaren decided to switch to Normec Foodcare Online's online QA system. “We chose Normec Foodcare Online because this system works with the latest technology,” says director Nico Sluis. "Normec Foodcare Online has a good link with our customers' data pool systems, such as PS in foodservice. The internal links are also good, for example between production and quality assurance. We don't have to transfer or copy any data. Everything fits together seamlessly. The system quickly provides us with the reports we need, for example per process, per department, per product group, or per person."
Normec Foodcare Online has a good connection with our customers' data pool systems, such as PS in foodservice.
User-friendly
Nico Sluis Vleeswaren will be working with virtually all modules of the application, including e-learning, inspections, the quality manual, and specifications. The company started using the inspection module in January. “The implementation went very quickly,” says Sluis. "The entire inspection system was up and running within a day. The system is user-friendly. For example, we can easily add items to our inspection rounds. We don't need a system administrator for that." Nico Sluis Vleeswaren carries out the inspection rounds using a tablet. This ensures that the data is entered into the system correctly and immediately. A dashboard displays a single central action list. This gives the company an overview of the current status at a glance.
The entire inspection system was operational within a day.
Small business
Nico Sluis Vleeswaren will also be implementing the other modules in the near future. “I think it's important to work with a single, uniform system,” says Sluis. “We're introducing it step by step.” Nico Sluis Vleeswaren is a relatively small company with around 25 employees. Nevertheless, Sluis does not consider such a comprehensive automation system to be an unnecessary luxury. "A good automation system prevents employees from spending days manually entering data or copying it from one file to another. The online QA software is inexpensive. We will quickly recoup the cost of the system. What's more, an automation system reduces the risk of errors. We work to the highest standards in our company. For example, we are BRC-certified at AA level. Normec Foodcare Online helps us maintain this high level."
More about Normec Foodcare Online
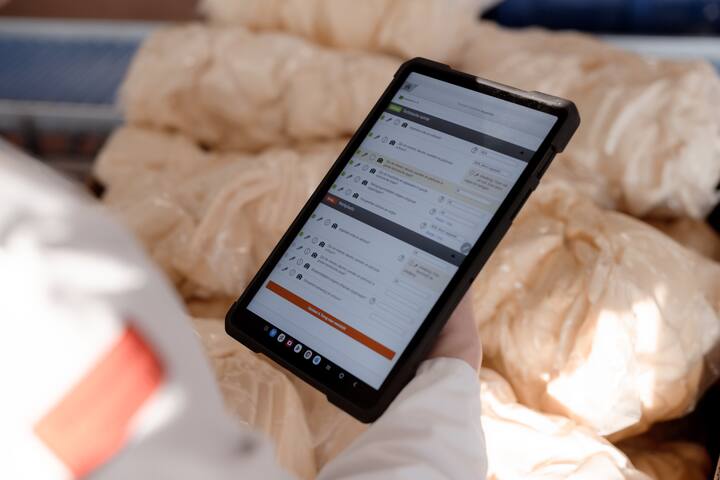
Normec Foodcare Online
's-Hertogenbosch Netherlands