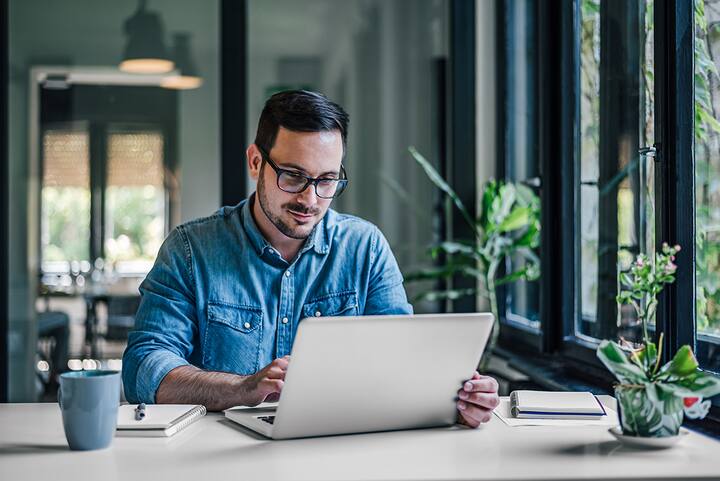
Simons Vleeswaren about Normec Foodcare Online
Improving food safety culture for Simons Vleeswaren
Simons Vleeswaren has been conducting digital inspections via our online inspection module since 2020. This not only makes work within the company more efficient, but has also improved the food safety culture. QA Manager Robin Havenith explains what digital inspection means for the company and what you need to pay attention to.
Need for an efficient, user-friendly, and centralized system
In mid-2020, Simons Vleeswaren approached us to provide a demo of the Inspections module. They needed a simpler and more efficient way to perform, complete, and analyze inspections. Robin explains: "In the past, we used an Excel document in which all comments, points for improvement, deviations, photos, etc. had to be entered manually. This was very time-consuming and prone to errors, given the choices of all the mandatory fields and the photos that had to be uploaded, saved, compressed, inserted, and dragged and dropped. In addition, the document was managed by the Quality Department, which meant that feedback from action holders had to be entered manually, resulting in duplication of work. There was a need for an efficient, user-friendly, and centralized system."
For our organization, the transition to digital not only means improved efficiency, but also the collection of data that is valuable for improvement projects and objectives.
A breath of fresh air to work with this package
Since mid-2020, the company has been working with the inspection module at two locations. Employees schedule inspections via the online business application in Normec Foodcare Online and carry out the inspection rounds using the inspection app on the iPad. "It's a breath of fresh air for the inspector to work with this package. You can decide for yourself how to organize, schedule, carry out, and complete the inspection. You can enter the reasons for any deviations on the tablet right there on the spot. If you prefer not to do this, you can also do it at your own workplace or from home on your laptop after the inspection," adds Robin.
40% time savings
Once the inspection is complete, the report, including photos, is immediately ready and the statistics are updated. Robin: "We have achieved a time saving of 40% compared to the administrative processing we used to have to do. The action holders do have more work to do, but even more important is the extra awareness and involvement on the work floor that we have achieved. For our organization, the switch to digital not only means an improvement in efficiency, but also a collection of data that is valuable for improvement projects and objectives."
Improvement in food safety culture
A change has been noticeable throughout the organization since the introduction of digital inspections. "The food safety culture and quality culture have improved since the introduction of digital inspections. As the quality department, we now increasingly carry out inspections together with the department manager. During the inspections, topics such as personal hygiene, environmental hygiene, process hygiene, food defense, technical condition, and pest prevention are discussed. It is immediately ‘training on the job’ and improvements/deviations can be discussed in detail on the spot," says Robin.
The food safety and quality culture has improved since the introduction of digital inspections.
Extremely user-friendly
"The QA software was developed by QA professionals and is extremely user-friendly. Even for one-off recordings, such as floor repair work, reports can be generated in your own house style. The automatic reminder emails and notifications also make it very easy for the action holder to use. Just click on the link and you are immediately where you need to be,“ says Robin about the user-friendliness of the inspection module. ”The support department is also quickly available by phone and the support consultant can immediately look at your screen remotely. There is a lot of QA knowledge at Normec Foodcare Online, which means you are quickly on the same page."
The automatic reminder emails and notifications also make it very easy for the promotion holder to use.
Take sufficient time
Robin has a tip for other and future users of the Inspections module: "Take sufficient time to set up the module and check how each adjustment works in practice. If in doubt, ask Normec Foodcare Online for advice to achieve the best results. Come up with a clear plan, draw up clear instructions, and present the new way of working. This will prevent a false start."
About Simons Vleeswaren
Simons Vleeswaren was founded in 1976. At its modern production site in Roermond, the company produces a wide variety of halal meat products, both under its own brand and under private labels. Examples of products include halal luncheon meat, knakworst, garlic sausage, and sliced meat products. The company values quality, service, flexibility, continuity, and personal contact and is certified for the BRCGS and IFS food safety standards.
More about Normec Foodcare Online
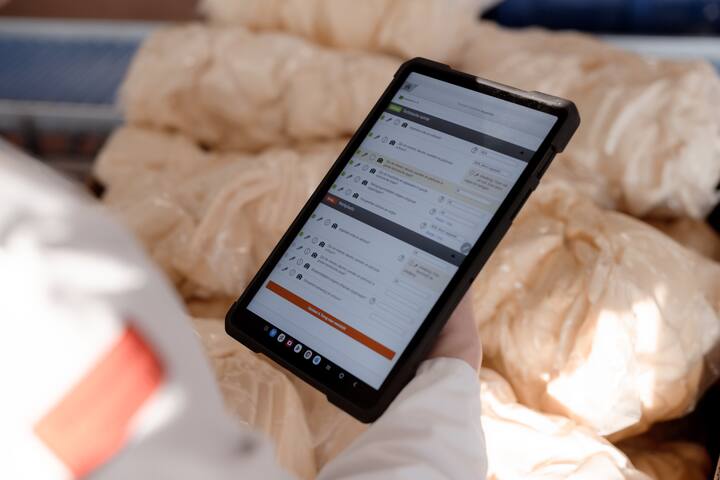
Normec Foodcare Online
's-Hertogenbosch Netherlands