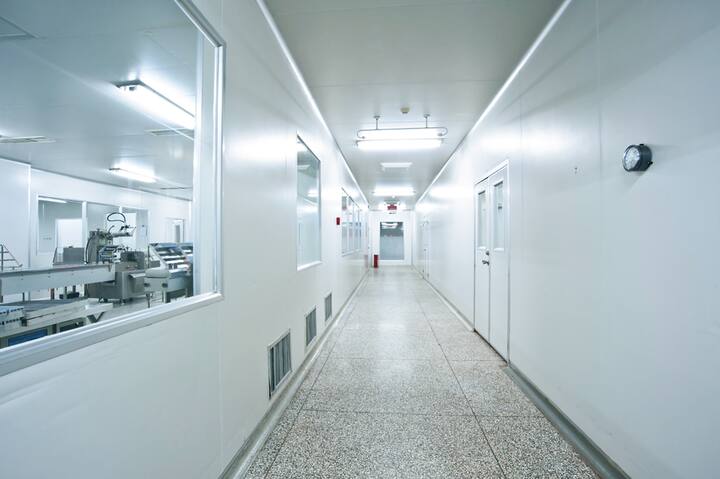
What is Involved in the Construction of a Cleanroom? | PIC/S Standard for Hospitals
A new Royal Decree was recently published, titled “Concerning the Preparation and Dispensing of Medicinal Products and the Use and Distribution of Medical Devices within healthcare institutions”. You can read all about it in the blog "The New Regulations for Hospitals and Their Pharmacies." In concrete terms, this means that starting from January 1, 2026, stricter requirements will also be imposed on the way medicines are prepared in hospitals. This is referred to as GPP, which stands for Good Preparation Practices. It is expected that work will be carried out in controlled environments, where the handling of open containers must always take place in ventilated areas with filtered air. In other words, hospitals will also be required to install and validate a cleanroom, along with the corresponding quality system, for their preparations.
There are several important questions a hospital should ask itself before beginning the construction of a cleanroom. Will the hospital’s cleanroom be used for sterile preparations, and does this include cytostatics, or are there other specific compounding needs or purposes, such as a fertility lab, for example? Everything starts with understanding your own processes and procedures.
Next, one should consider how these processes will be translated into the use of the cleanroom: aseptic working techniques, sterile gowning, waste flows, the number of staff using the cleanroom at the same time, and so on. All this information is typically gathered and visualised through process mapping, which then results in a User Requirements Specification (URS)—a detailed document outlining all user needs while taking into account the applicable regulations.
In addition to defining the requirements, it is also recommended to perform a risk analysis. This can be done, for example, through a Failure Mode and Effects Analysis (FMEA). An FMEA is a tool used to analyse a process or physical system in order to identify potential risks, and to then take steps to mitigate or at least minimise these risks. The main advantage of conducting a risk analysis is that it allows for targeted risk mitigation and, where necessary, elimination. This helps to avoid unnecessary costs and time loss during the project. Both a URS and a risk analysis are living documents that can evolve with the project and be updated through version control.
Following the requirements and risk analysis, a quality and/or validation plan is drafted. This plan outlines the approach to validation and the process to be followed in order to demonstrate that all requirements are met. This leads to the development of several protocols that describe in detail the necessary tests. These include, for instance, the validation of the cleanroom itself, such as microbial sampling, particle counting, pressure differential measurements, and airflow analysis.
A second protocol covers utilities and the corresponding tests, including the installed gas and water systems (e.g. PW, WFI, etc.). Another protocol focuses on the finishing of the rooms, with tests to verify the use of correct materials, whether the desired level of finish has been achieved, the absence of dirt traps, damages, and so on. Depending on what is further described in the URS, additional protocols may be needed — for example, the monitoring and alarm systems, testing of software packages, or validation of specific equipment such as laminar airflow cabinets, biosafety cabinets, or isolators.
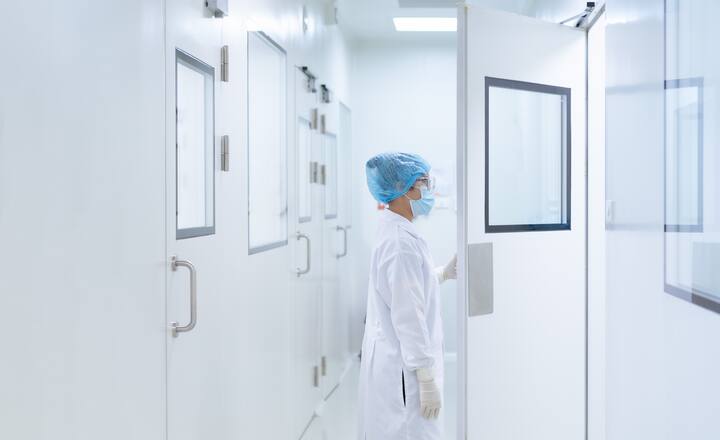
In addition to testing the installed cleanroom, utilities, software, equipment, and other critical systems, it is also essential to document all standard processes in Standard Operating Procedures (SOPs). Instructions must be provided for various operations, including entering the cleanroom, cleaning the cleanroom, and performing specific tasks. These SOPs are a crucial part of the quality management system and form the foundation for your Good Preparation Practices (GPPs). By verifying that all necessary SOPs are in place, the continuous quality of medicine preparation and delivery within a healthcare facility can be ensured.
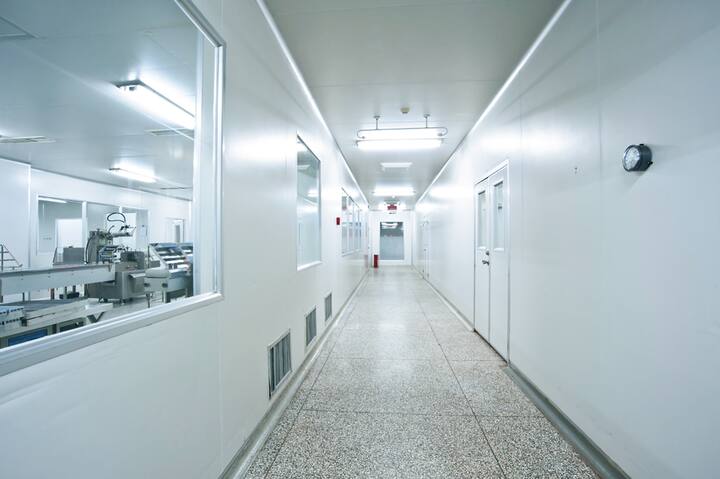
Once all tests have been completed, the results are compiled into separate validation reports for each system. These reports are then summarised in one overarching, consolidated report. This final report officially releases the cleanroom and its associated systems for use. From that point on, it is confirmed that work is taking place in a controlled environment that meets all requirements — both from the user and from regulatory authorities. This is referred to as an initial validation. To ensure that all systems continue to operate as intended, periodic revalidation of critical systems is carried out. This is done in accordance with the procedures established in the quality management system, including, among others, change control.
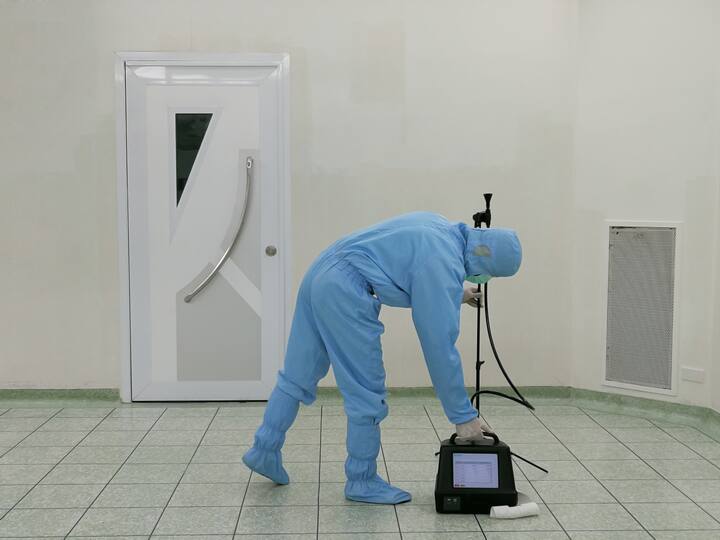
Cleanroom support through Cleanroom Implementation Blueprint (CLIMB):
Ready for the Future?
Is your organisation ready for the future of pharmaceutical and high-tech manufacturing? For many hospitals, laboratories, start-ups, and other organisations, building and validating a cleanroom in accordance with (new) regulations can be a significant leap into the unknown — often lacking the necessary in-house expertise.
By partnering with Normec Advipro, you gain access to targeted expertise and support to successfully complete your cleanroom project. Ensuring quality during the implementation of changes and improvements in an innovative and validated production environment is essential. This contributes to improved long-term cost efficiency, as every decision can impact the final commissioning.
Based on this experience, Normec Advipro has developed its own Cleanroom Implementation Blueprint (CLIMB), designed to advise and support cleanroom project teams throughout the entire process — delivering the necessary tools and documentation at each stage.
More about Normec Advipro
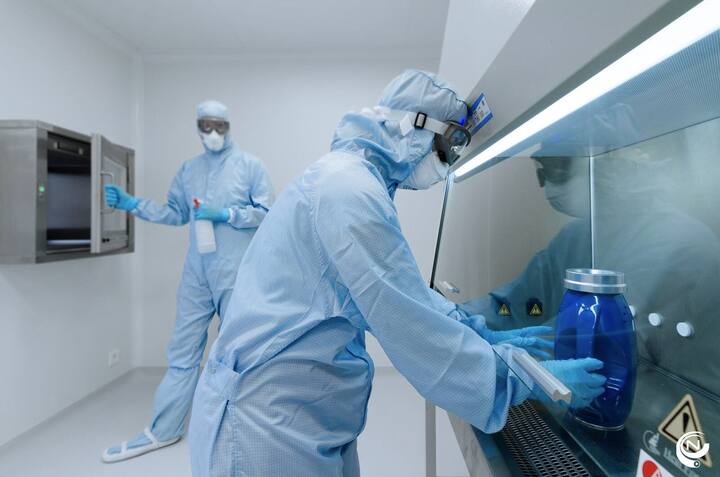
Normec Advipro
Lille Belgium