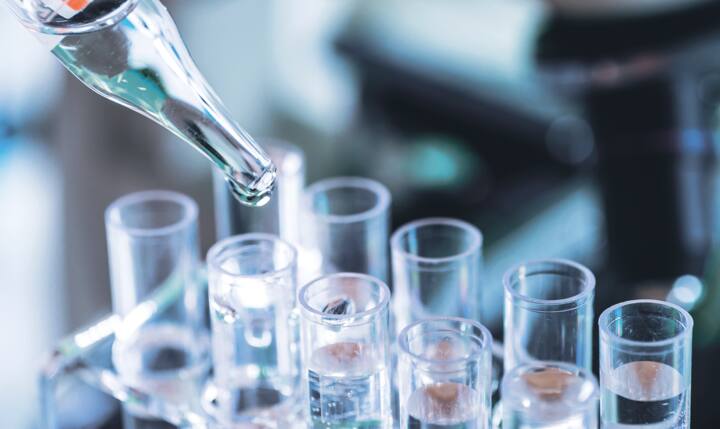
StarCuisine about Normec Foodcare Online
More insight and higher scores for StarCuisine
As an oriental specialist, StarCuisine prepares traditional recipes using traditional methods. The company has various certifications, such as FSSC 22000, SKAL, and Halal, and strives for the highest quality. At the beginning of this year, StarCuisine launched digital quality assurance via the Inspections module. This has enabled the company to make significant improvements. One of the quality assurance staff members talks about their initial experiences with digital inspections.
Why did you start looking for a digital solution?
“Our production rounds used to be so cumbersome. We would walk around, take photos, and enter everything into a homemade Excel file. We did end up with a score, but it took a lot of extra work. We did send the Excel file, but the photos, for example, were not visible to production. As a result, production employees never really knew what issues we were encountering. And then we thought: there must be an easier way that takes less time.”
You really gain a lot more insight. Not only per department, but also per subject.
You are now conducting inspections using the inspection app. What are the differences compared to the old method?
“We have now split the large production rounds into separate lists for the different departments. This gives each department a clear overview of what is going on, including photos and additional comments. It simply works much better, faster, and is more organized. In production itself, you notice that employees really get to work when they receive the report. They look at the report, see the photos, and try to resolve the issue as quickly as possible. They are more motivated to take action. We now send the report to all departments. Ultimately, we want all departments to have their own login for the QA Software so that they can resolve any issues themselves, but we are not there yet."
What has digitization brought to the organization?
“We have definitely saved time by working with this module, but above all, we have made the information more visual. And I actually find that even more important than the time savings. The frequency of inspection rounds has increased thanks to the use of the Inspections module. We used to do one round per month. Now we do them weekly, so we can see the scores every week. As a result, the scores are generally a bit higher. We can see more clearly what is going wrong. Because you can see statistics immediately, it is easier for management and for ourselves to see what we need to pay attention to. Should we pay more attention to general hygiene or personal hygiene? And how are the registration forms being filled out? This also allows management to see which registrations are going well and which are not. They have a better idea of which areas need attention. You really gain a lot more insight, not only per department, but also per topic.
As a result, the scores are generally somewhat higher. We can see more clearly what is going wrong.
How do employees feel about the increased inspection frequency?
“Of course, it's still the case that you're checking the work. Beforehand, I was afraid that people would think we were being too strict. But our colleagues actually see it more as a challenge. The moment you walk into the department, you hear them say: ‘This time we've got 100%, right?’”
More about Normec Foodcare Online
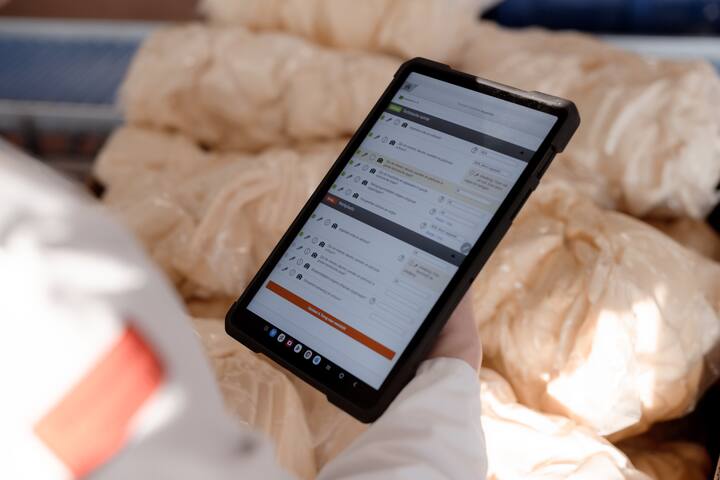
Normec Foodcare Online
's-Hertogenbosch Netherlands